Email: info@fibremetrics.com



Rapid measurement of fiber diameter
Diamscope
Diamscope is the world's first automatic rapid image analysis system to measure fibre diameter snippets from 0.5 to 50 microns (um). Measuring up to 20,000 fibres per minute, it provides measurements for mean diameter, distribution of diameter, mean curvature and distribution of curvature. It is ideal for measuring glass, ceramic, synthetic and carbon fibres.
​
Accurate
-
0.2um to 80um fibre diameter range.
-
Curvature distribution and mean.
-
Length distribution up to 0.5mm.
-
High repeatability.
-
No operator bias from measurements.
Fast
-
Up to 20,000 fibre snippets measured per minute.

Diamscope Technology
Samples are prepared by cutting a sample to 0.7mm fibre length over the measuring bowl. The bowl contains 120ml of distilled water.
Spreadsheet output with 0.2um resolution diameter histogram as shown below. High precision data is stored for future use.
After each measurement, the bowl is automatically rinsed and refilled. The fibres are filtered and the water is stored in a reservoir to be reused.
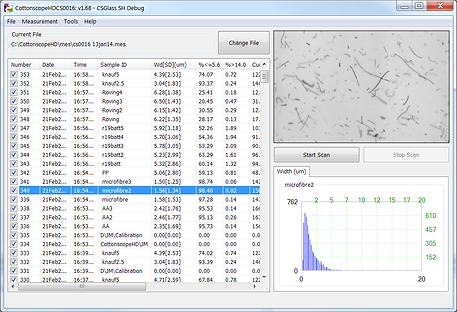
Key benefits of Diamscope
At present, curve measurement in glass fibres is new and the subject of research, since a high speed curve measurement device has not been previously available. However, a number of papers are available from www.ofda.com that discuss OFDA curvature in wool.
Fibre curvature is the measurement of the degree of bend of the fibre snippet in degrees per mm (deg/mm). Mean values range from 1 deg/mm to more than 100 deg/mm. Fibre curvature has a good correlation with bulk and therefore provides better control for insulation and compression recovery properties.
​
Diamscope provides the following benefits:
-
Manufacture superior fibre that meets strict specifications and satisfies customers' high performance requirements.
-
Greater control of fibre quality and avoidance of costly mistakes at the manufacturing stage.
-
Reliable monitoring and timely detection of defects for scheduling repairs and maintenance.
​
​
